Reference
Tantalum: The Hidden Treasure of Modern Metals
Tantalum: The Hidden Treasure of Modern Metals
For many of us, the very first encounter with a tantalum watch is a bewildering experience. The initial reaction is often one of surprise at its unexpected heft. While it has a colour reminiscent of titanium, it has a premium weight. This is quickly eclipsed by the sticker shock – the startlingly high price that can, at times, surpass platinum and gold.
Yet, tantalum is not classified as a precious metal, nor is it anywhere as rare as gold or platinum in the Earth’s crust. The high cost of tantalum watches is driven not by the metal’s inherent rarity but by the technical challenges associated with machining this complex material. Its enigmatic mixture of characteristics – gold-like density, copper-like ductility, steel-like thermal conductivity, and tungsten-like melting point – makes it notoriously difficult to work with, resulting in tantalum watches being far rarer in the practical sense.
Its unique attributes has a special bearing on what constitutes value or “preciousness” in watchmaking. In fact, it fits neatly within the broader conversation on the secondary market where historical significance and scarcity often outweigh the unseen effort and – often very visible – complexity involved in a watch’s creation – a dynamic that ultimately fuelled the rise of “hype watches” where perceived value eclipses intrinsic worth. In many ways, it is a reminder that value is to be found in the unseen effort, not just in a metal’s or watch’s rarity, brand cachet or the weight of history behind it.
Where gold flaunts and platinum asserts, tantalum intrigues. It doesn’t possess the striking visual impact of gold or the same prestigious weight of platinum, but the very fact that it has eked out an existence as a watch case or bracelet is a quiet marvel that shouldn’t be ignored.
Rarity, Supply and Market Dynamics
To begin, it’s interesting to consider what makes a metal “precious.” The nature of preciousness is multifaceted, determined by a combination of rarity, difficulty of extraction, physical properties, market demand, and historical and cultural significance.
Gold has been cherished for millennia for its beauty, malleability, and resistance to corrosion. It’s not the rarest metal, with an abundance of around 0.004 parts per million (ppm) in the Earth’s crust. Metals such as rhodium and osmium are significantly rarer than gold, approximately 0.0007ppm and 0.0001 ppm respectively. However, the historical role of gold in currency, jewellery, and culture has solidified its status as a marker of wealth.
Platinum is slightly more abundant in the Earth’s crust at 0.005 ppm but is more geographically restricted in terms of mining, harder to extract, and its production more concentrated. This makes it more valuable in other aspects despite its slight greater availability in nature.
Gold is mined in many countries, including China, Australia, Russia, and the United States. Platinum, however, is primarily mined in a few regions, with South Africa accounting for the majority of global production, followed by Russia and Zimbabwe. This geographic concentration adds to platinum’s rarity and makes its supply more vulnerable to disruptions such as geopolitical conflicts. Gold is often found as nuggets in its native form but it is also extracted from ores through processes like cyanidation, amalgamation, or smelting, followed by purification methods like electrolysis or refining with acids. Platinum is commonly found in ores alongside other platinum group metals (PGMs) such as palladium, rhodium, iridium and osmium. Its refining process is more complex due to the need to separate it from these chemically similar metals, requiring multiple stages of extraction and purification.
As a result of these factors, global annual production of platinum is significantly lower than that of gold. Roughly 3,300 metric tons of gold are mined each year, compared to about 190 metric tons of platinum. Gold is abundant enough to support a broad and liquid market, making it more accessible and effective as a store of value compared to platinum. Consequently, gold is often seen as a reliable hedge against inflation and economic instability, which helps explain its high current price.
Tantalum, with a crustal abundance of about 2 ppm, is far more common than both gold and platinum. Tantalum is typically formed through geological processes where molten rock (magma) cools and crystallizes. It is commonly found in the mineral tantalite, part of the coltan ore group, and often occurs alongside niobium in pegmatite formations – coarse-grained igneous rocks formed deep within the Earth’s crust.
The extraction of tantalum involves mining pegmatite or alluvial deposits where the mineral has been eroded from its original source and deposited by water. The ore is processed through methods like gravity separation and flotation to concentrate the tantalum. After concentration, the tantalum-containing minerals undergo chemical processes such as leaching and reduction to extract pure tantalum metal. Because tantalum doesn’t occur in large, pure deposits, its extraction and refining can be labour-intensive and costly. Since the early 21st century, tantalum mine production has shifted from its previous dominance in Australia and Brazil to Africa. Countries like the Democratic Republic of the Congo and Rwanda are now the largest source of tantalum.
Tantalum is a highly refractory metal, known for its extraordinary resistance to wear, heat, and corrosion. It is biocompatible and has a very high melting point of 3017°C (5470°F), which is the fourth highest among metals. Due to these qualities, tantalum is primarily used in specialized industrial applications, such as vacuum furnaces, nuclear power plants, missiles, aircraft, surgical sutures and implants as well as capacitors with the latter accounting for about 50 percent of its consumption.
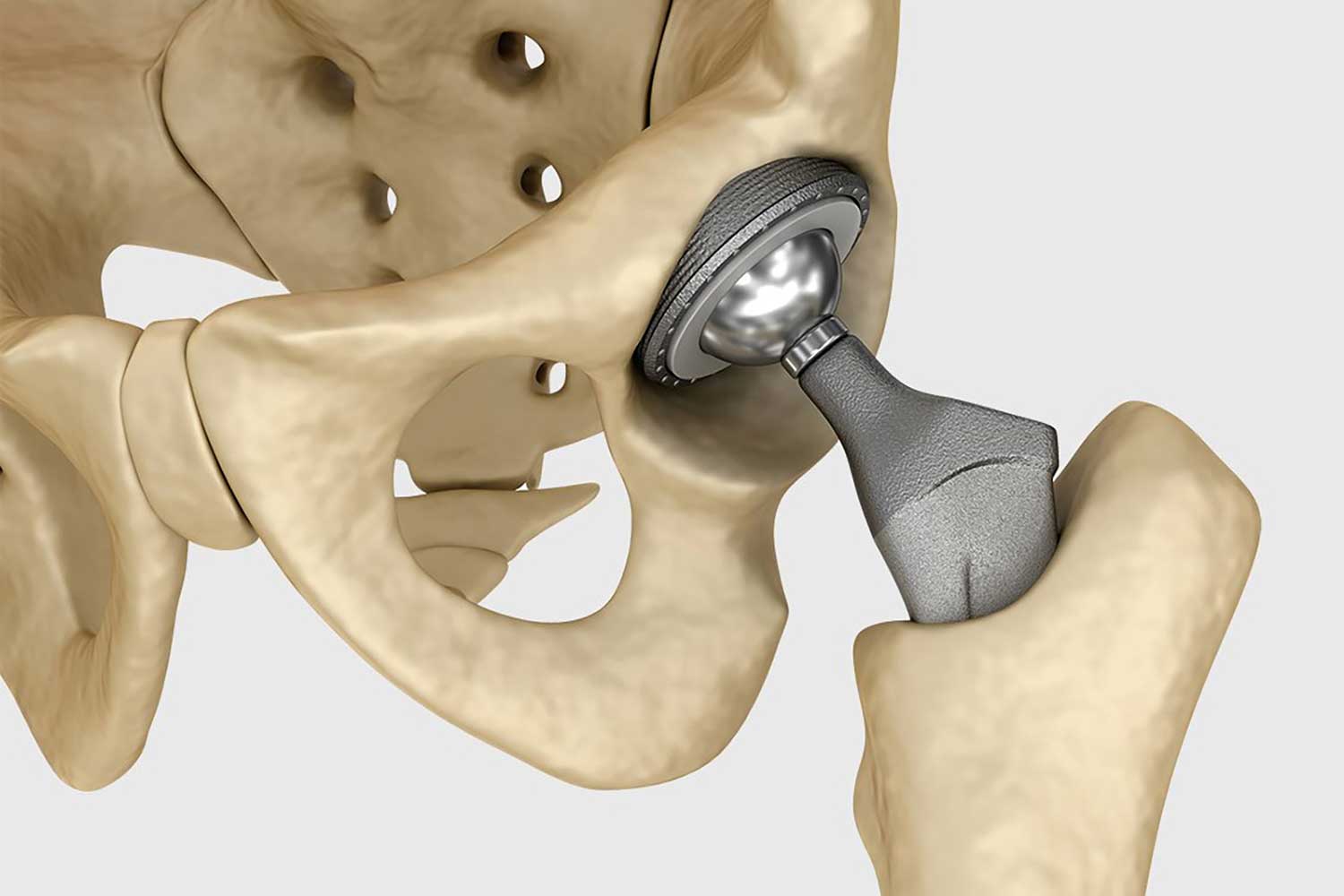
Tantalum is widely used in reconstructive surgery due to its exceptional biocompatibility, corrosion resistance, and ability to promote bone ingrowth. Tantalum orthopedic implants, such as acetabular cups, have high volumetric porosity, which allows bone tissue to grow into the implant’s structure, enhancing stability and long-term fixation
Its specialized use and complex supply chain limits the breadth of its market. As a result, it does not have a futures market and is typically traded through direct long-term contracts or niche markets, rather than major commodity exchanges. As of September 6, 2024, the spot price of gold is approximately $2,506 per ounce (or $88,402 per kilogram), and platinum is priced at $919 per ounce (or $32,421 per kilogram). In contrast, tantalum is priced significantly lower at around $313 per kilogram.
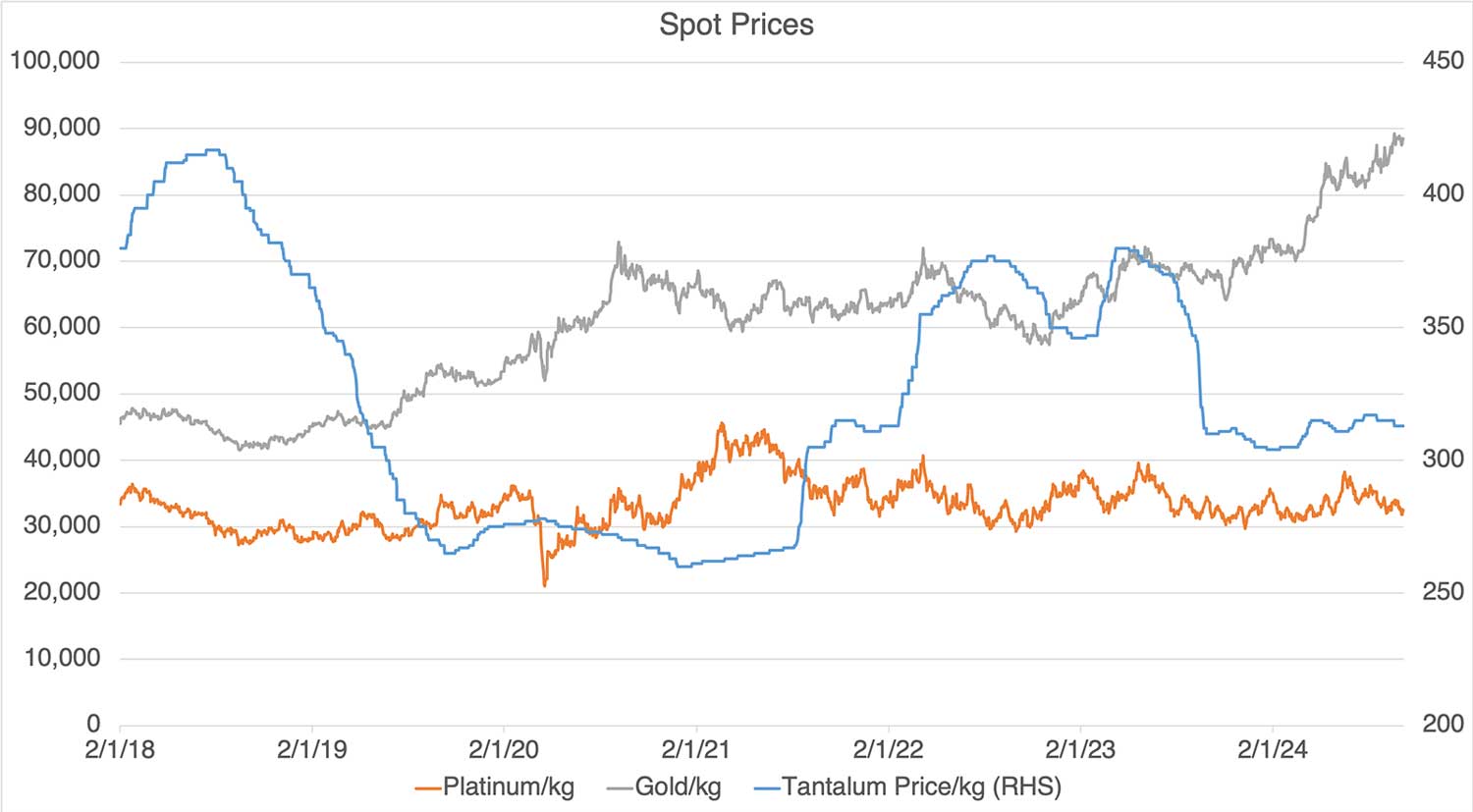
Spot prices of gold stands at 2,506 USD/ounce or 88,402 USD/kg as of Sep 6 2024, while platinum is at 919 USD/ounce or 32,421 USD/kg. Tantalum (on the right) is priced way below these precious metals at 313 USD/kg. That aside, since 2018, the spread between gold and platinum has widened from under 400 USD/ounce to 1,587 USD/ounce. (Graph: Revolution; Sources: Investing.com for Tantalum, Macrotrends For Platinum, Bloomberg + Ice + Datastream + World Gold Council for Gold)
Tantalum in Watchmaking
Tantalum is increasingly embraced in watchmaking for several reasons. First, its beautiful blue-grey hue offers a striking and contemporary aesthetic that aligns with the modern concept of luxury. It has a satisfying weight that contributes to a feeling of quality. It also boasts superb technical qualities that make it a great material for cases and bracelets. Notably, it has a greater resistance to corrosion compared to gold and platinum, capable of withstanding some of the deadliest of acids including aqua regia – Latin for ‘royal water’ – a mixture of concentrated nitric and hydrochloric acids capable of dissolving ‘kingly’ metals like gold and platinum. Interestingly, it was this remarkable chemical inertness that inspired its name.
Discovered in 1802 by Swedish chemist Anders Gustav Ekeberg, tantalum was named after the mischievous Greek demigod Tantalus, who was condemned by Zeus to stand in a pool of water that receded every time he tried to drink, while fruit-laden branches above him withdrew whenever he reached for them. The name reflects the metal’s challenging property of resisting dissolution, as its oxide proved impervious to acids.
In terms of physical attributes, tantalum has a density of about 16.6 grams per cubic centimeter (g/cm³) and a Mohs hardness of about 6.5, making it harder but less dense than both pure gold and platinum. Gold’s softness makes it easy to work with, but it has to be alloyed with other metals to increase its strength for practical uses. Pure gold has a density of about 19.3 g/cm³, but 18k gold, which is alloyed with other metals, has a density of approximately 15.6 g/cm³, making it less dense than tantalum. The Mohs hardness of 18k gold is around 2.7-2.8. Platinum is denser than gold, with Pt950 (a common platinum alloy consisting of 95% platinum and 5% other metals designed to increase its hardness) having a density of about 19.2 g/cm³. Its Mohs hardness is around 4.5, making it more resistant to scratches and wear compared to gold.
Another valuable trait of tantalum is its hypoallergenic nature. It is biologically inert, making it suitable for people with sensitive skin and metal allergies, unlike many alloys that include common allergens such as nickel and copper. For instance, 316L stainless steel and white gold contain nickel while yellow gold and rose gold contain copper. Titanium, while being biologically inert, tangentially similar in colour and generally harder than tantalum in its Grade 5 alloyed state, remains lightweight and lacks the weight and feel that tantalum offers.
However, tantalum’s unique characteristics and how they relate to one another present significant challenges in machining. It exhibits a “sticky” behavior during cutting and tends to adhere to the cutting tool instead of being cleanly sheared away. As a result, instead of producing small, manageable shavings, the cutting action generates thick chips.
Additionally, its high melting point generates substantial heat during machining due to the larger cutting forces required. In contrast, metals with lower melting points are generally easier to shape and mold. The excessive heat, in turn, leads to rapid wear and damage to standard machining tools, which must withstand these extreme conditions. Furthermore, tantalum has relatively low thermal conductivity (~57 W/m·K while platinum is 71 W/m·K), meaning that while it can conduct heat, it does not dissipate it effectively. This results in localized heating, further exacerbating tool wear.
Additionally, its chemical inertia means it does not readily interact with most machining fluids, necessitating the use of specific techniques and fluids designed for such inert materials to prevent issues like poor cooling. This requires adjustments to machining techniques to manage the effects effectively.
As a result, machining tantalum demands significant expertise and sophisticated techniques to handle its unique challenges and achieve the desired precision and finish.
The History and Trials of Working with Tantalum
Although tantalum, particularly in dress watches, has gained momentum only in recent years, its use in watchmaking stretches back to the 1980s – a period marked by significant exploration and expansion of tantalum deposits particularly in Australia.
The earliest known watch to be created in tantalum was an Audemars Piguet Royal Oak, commissioned by King Juan Carlos of Spain. The King had sought a version of the Royal Oak with a more subdued appearance to prevent reflections from scaring off his prey during hunting. He had previously given one of his Royal Oaks to his gunsmith, who attempted to apply a bluing technique similar to that used on hunting rifle barrels, but the results were unsatisfactory. Eventually, he turned to Audemars Piguet, who then devised a solution by using tantalum, known for its natural dark grey-blue lustre, to achieve the stealthy tone the King desired.
The first tantalum watches to be produced in series were two quartz-powered Royal Oak models in 1988, the 33mm two-tone Royal Oak ref. 56175TR, which combined tantalum with rose gold and the ref. 66270TT which paired tantalum with titanium. They were soon followed by the 35mm self-winding ref. 14486TR, introduced a few months later. These Royal Oak models had a tantalum case and bracelet while their bezels and intermediate links were in a contrasting metal. The brand also introduced the Huitième 25644TR chronograph that same year which came in a large 40mm case in tantalum and rose gold.
A year later, Jaeger-LeCoultre introduced the meca-quartz Odysseus Chronograph with a tantalum case at Basel Fair. A Jaeger-LeCoultre press release from that year stated: “Jaeger-LeCoultre has mastered the secret of working the most secret of metals in the world […] The hardness and imperviousness of this metal, and therefore its high resistance to heat and chemicals, posed a challenge to researchers. Up until now, it had only been used in simple components, with its resistance to stamping, machining, and finishing proving especially daunting.”
The release continued in a dramatic and triumphant tone, “The efforts at Jaeger-LeCoultre to work this diabolical metal have not remained ‘tentative.’ The Odysseus, in its glittering blue case, as finely polished as gold and adorned with massive rose gold accents, marks the end of an epic struggle. It cannot escape the attention of collectors who recognize a rare piece uniting the finest watchmaking technology with exceptional materials.”
In 1993, Omega introduced the Seamaster Diver 300m Chronograph (ref. 2296.80.00) with a titanium case on a tri-colour, tantalum, titanium and rose gold bracelet. The primary links were in titanium but the twin centre links were a sandwich of polished rose gold and brushed tantalum. In 2018, the brand paid tribute to the exotic watch with the tri-colour Seamaster Diver 300m (ref. 210.60.42.20.99.001), released in a limited edition of 2500 pieces. This time, its bezel along with centre links, were made in tantalum while the crown, bezel ring and helium escape valve were in Sedna gold. The tri-metal theme continued in 2020 with the Seamaster Diver 300m Chronograph (ref. 210.60.44.51.03.001), once again combining tantalum, titanium, and Sedna gold. The watch remains in production and features a numbered case.
Both Hublot and Panerai have also explored the use of tantalum. Part of the uniqueness of tantalum is its inherent versatility. Its unassuming colour along with its extreme resistance to corrosion have made it the ideal material for sports watches but its luxurious heft also renders it equally ideal for dress watches. While platinum, gold, steel and titanium can be used in both contexts – these days, anything goes – tantalum tends to crossover more naturally.
The first use of tantalum in a time-only, manual-winding dress watch was in 2009. François-Paul Journe explains, “I’ve always wanted a collection with a blue dial and I couldn’t manage to make it. In 2007, with the Cadraniers de Genève, we found the solution. I asked what metal would go well with this dial, and tantalum was chosen – the Chronomètre Bleu was born.”
“As the Chronomètre Bleu was successful, I was asked to make other models in tantalum. I always refused, because the difficulty of manufacturing and the time available meant that we couldn’t meet these requests.” He continues, “So I decided to make a Tantalum concept for Only Watch only, in order to raise as much money as possible for medical research.”
Since 2015, Journe has created five one-of-a-kind watches for Only Watch which carried on the theme of the Chronomètre Bleu, featuring blue dials with tantalum cases, often going for multiples their estimates. For Only Watch 2023/24, he introduced the Chronomètre Furtif Bleu, which featured a tantalum bracelet for the first time. The watch hammered for CHF 2 million on a high estimate of CHF 440,000.
A casemaker at Journe’s case manufacture Boîtiers de Genève explains, “Tantalum is a very difficult material to machine. It is not possible to make small machining passes of less than 0.1 mm. There is very pronounced wear on the cutting tools.”
He continues, “Tantalum cannot be repaired using laser welding and cannot be polished using traditional methods. We homogenize the material using a special process, and we have developed a polishing method that is a Boîtiers de Genève manufacturing secret.” Nathan Bailly International PR Manager at F.P. Journe adds, “This polishing technique has taken years to perfect, with the right speed of rotation and the right polishing discs and pastes.”
“Tantalum gives off a lot of heat which tends to break the tools; moreover, the tools used are more resistant than those used for gold, for example, which are also used for platinum, and are therefore more expensive. CNC rotation speeds need to be reduced to limit the risk of breakage. We always machine tantalum under supervision,” he explains.
Another independent watchmaker who produces tantalum cases is Kari Voutilainen, who first created a unique Tantalor Decimal Minute Repeater in 2020. “It was such a nightmare to fabricate and it took a very long time to complete. I discovered that it is impossible to turn this metal on a lathe. The cutting tool just don’t make any chips. The metal is just rolling in front of the cutting tool and tool wears out immediately. It must be sharpened all the time. After every single sharpening, a new tool setting must be carried out.”
When it comes to milling tantalum, Voutilainen says, “It is possible but we must change tools all the time as they disappear.” Milling platinum is easier. “As a reference, platinum is 3/10 in terms of difficulty while tantalum is 10.” The challenges don’t stop there, he explains, “Threading the metal, though doable, it is ‘crispy’. Threading tantalum is 10/10 while platinum is 8.”
“Creating a tantalum case takes a huge amount of time. It requires a lot of work, but the final result is beautiful. It looks good and feels like a silk.” Voutilainen has since created tantalum cases for other brands, including Sartory Billard. In terms of pricing, he offers platinum and tantalum cases at the same price.
When the Grönefeld brothers introduced their first chronograph, the 1941 Grönograaf in 2022, the case material of choice was the defiantly inert metal, following persistent requests to their case maker.
Bart Grönefeld recounts, “The first time I saw a tantalum watch was in the mid-90s. A friend of mine owned one, and I immediately fell in love with its weight and colour. I asked if he’d sell it, and I ended up buying it. The model was an Audemars Piguet Royal Oak ref. 14800TR. With a diameter of only 36mm, it was a bit small for my wrist, so I didn’t wear it often. However, it remains a treasured piece in my personal collection.”
He continues, “When I researched the metal, I was also fascinated by its chemical inertness and high melting point of 3017°C. What I didn’t like was the quality of the polishing on the case. However, the Audemars Piguet was a pre-owned watch and may have been hastily polished by a less skilled watchmaker.”
“In 2018, we launched our brand. The GTM-06 was available in gold and platinum. When developing our second watch, the One Hertz, we found a new case maker and requested a Tantalum case. They refused due to the challenges of achieving a high-grade polish and finish. When launching our fourth model, the 1941 Remontoire, another new case maker also declined to work with Tantalum for the same reasons. After years of collaboration, we begged and persuaded them to investigate the feasibility of making a tantalum case for our 1941 Grönograaf. Thanks to our strong relationship, they accepted the challenge and succeeded in enhancing their skills to produce a perfect quality watch case.”
Joshua Shapiro, who launched his 26-piece Infinity Tantalum series in 2021, did the unimaginable: engine-turning on tantalum. “I tried guilloché on platinum, and the results were not good. Guilloché on tantalum is awful. The result is like dragging your finger through play dough. We successfully did guilloché on our tantalum chapter rings for the Infinity Tantalum limited edition, but only with the ratchet border pattern. That seems to work well because it forms the tantalum more than it cuts it.”
Shapiro explains, “If you imagine skinning an apple with a sharp knife. The peel of the apple will come away easily from the knife. Now imagine using a kitchen knife to remove the bark from a tree. The bark will not want to come away and the knife will become dull very quickly. It is the same issue with tantalum, the chip does not want to leave so the cutting tools on a mill or lathe become dull or break much, much faster than with a material like stainless steel, brass or gold.” He continues, “For instance a single endmill could last for 20 cases in stainless steel but maybe only 1/3 of a single case in tantalum.”
“The best and most efficient way to work with tantalum is to bypass using cutters all together and stamp it, but setting up stamping processes is extremely expensive and cumbersome for low volume. Stamping also helps with polishing the cases. The harder the state tantalum is in, the better it polishes, and stamping makes tantalum much harder.”
He explains, “We use carbide tooling for tantalum with special coatings.” While polishing tantalum is often said to be comparable to platinum, Shapiro clarifies, and his final remark is worth writing in bold: “Polishing tantalum is most similar to polishing platinum, but much, much worse. We have been refining our process for years. Achieving a good polish on tantalum is one of the most difficult tasks in watchmaking.”
James Kong, co-founder of Fleming, shares the same sentiment, having created a tantalum limited edition of their debut watch, the Series 1. “We’ve found producing a tantalum case to be much, much more difficult than producing even a platinum case. Tantalum is harder on tooling, much more difficult and labour-intensive to polish, and casemakers have much less occasion to work with it, so even the few casemakers that have worked with it generally still have things to learn through trial and error when crafting a specific case design out of tantalum for the first time.”
“Many suppliers in Switzerland will simply decline to work with tantalum. We were lucky enough to find a single casemaker in Switzerland who was willing to take on our case, which involves polished and faceted lugs, an alternating brushed and polished case band, and a polished bezel,” he explains. “Even then, it took almost two years and a number of attempts, scrapped runs, and case re-engineering before we achieved a result we were all happy with. Achieving a polished finish equal to that of our platinum and gold cases was the most difficult part, so we’re very grateful to our casemaker for what they were able to achieve and for sticking with us.”
“In terms of overall cost, we’ve found working with tantalum is comparable or more expensive than platinum, despite tantalum not being a precious metal; while the raw materials cost is lower, the cost to work in tantalum is much higher, and significantly more expensive than to work with steel, especially when polishing is involved.”
Recently, Shapiro, Fleming and Ming, announced the formation of Alternative Horological Alliance (AHA), which allows each brand to leverage on their collective expertise, explore new concepts and create unique offerings that might not otherwise make economic sense for any one brand to pursue alone. To prove their point, their first collaborative project is a five-link tantalum bracelet, which will be produced with 19mm, 20mm, or 21mm end links to be fitted to watches from all three founding members. The bracelet was designed by Ming and produced by Shapiro. “The bracelet was challenging in tantalum because Ming’s design is organic with many small links. A flat link bracelet would have been significantly easier,” says Shapiro.
While all of this gives you a general idea of how demanding the metal is to work with, it’s difficult to gain a full understanding of the alchemy involved at different stages in the production of cases and bracelets without feeling like you are treading on proprietary ground. The immense difficulties involved make every triumph a claim to fame, keeping these methods closely guarded. But the next time you come across a tantalum watch, know that the choice of metal was far more than an afterthought; mechanics of timekeeping aside, it is itself a showcase of technical prowess, hidden in plain sight.