Technical
Gear Design: The Backbone of Watchmaking
Gear Design: The Backbone of Watchmaking
Gear design in watches is something we give very little thought to. It is virtually invisible until an anomaly arises, such as when a chronograph seconds wheel is devoid of micro gearing in a bid to cut costs or when a ratchet or crown wheel showcases perfectly polished wolf’s teeth or when a differential is constructed with full-fledged bevel gears like those found in the drivetrain of a car. It’s a curious blind spot, considering that without gears, the balance wheel — the all-important heart of the watch — would be nothing more than a wheel. Even quartz watches aren’t spared, as they still require gears to convert impulses from the stepping motor into the precise motion that drives the hands.
Admittedly, this is a topic that has been on the back burner for quite some time, as nearly every other subject that crops up tends to feel instantly more pressing or exciting by comparison. Yet, in truth, few things are as quietly indispensable.
The fundamental purpose of gears is to transmit rotary motion from one shaft to another. However, the number of teeth selected and how a tooth profile is designed can make a great difference to the global efficiency of a movement. As each tooth transfers torque from one point to another, minor fluctuations occur, and this effect compounds across the gear train, ultimately influencing the amplitude of the movement.
At its core, a tooth profile must be conjugate to another tooth profile to ensure smooth motion and continuous engagement. This conjugate action means that as one tooth moves, it drives the other tooth without slipping. The gears that make up the wheel train, motion works and keyless works of a watch are designed to address different conditions within a movement.
However, the design of gears often involves trade-offs to meet additional requirements such as ease of manufacture and tolerance of errors. The best gearing, therefore, cannot be strictly defined; instead, it must be understood as a balancing act between theoretical efficiency, practical considerations and at times, beauty. Hence, it must be said that this is not intended to serve as a guide on how gears in a watch should be designed or evaluated but rather to provide an insight into this balancing act and what brands, watchmakers and constructors are doing with their gears today.
To gain a deeper insight into the state of gear design, we spoke to Valérien Jaquet founder and CEO of Concepto and gear specialist Jérémy Freléchox, co-founder of Timeforge and Vanguart Watches and a former APRP member of 15 years.
Jérémy emphasized early in our conversation that “there is no proper training for gear design. Usually we have general theory at engineering school and practical courses at watchmaking schools like how to rebuild a missing tooth during restoration and what to be aware of. So people do seek the help of specialists when facing a gear problem.”
The Basics of Gear Design
At the heart of gear design lies the pitch circle—an imaginary circle that represents the effective contact point between two meshing gears. The diameter of this circle, known as the pitch diameter, is a critical factor in determining the gear ratio. The gear ratio defines how many rotations the input gear must make to turn the output gear once. It is calculated as the ratio of the number of teeth or the pitch diameter of the output gear to that of the input gear.
The pitch diameter and tooth count of each gear work together to shape the behavior of the gearset, affecting both its torque transmission and speed reduction or amplification. Gears with larger pitch diameters or more teeth rotate slower but deliver greater torque, while smaller pitch diameters or fewer teeth result in faster rotations with less torque. The gear ratio of a wheel train is designed to convert the slow rotation of the mainspring barrel into the high-speed motion required to drive the escapement. The fourth wheel completes 60 rotations for every single rotation of the center wheel, establishing a gear ratio of 1:60.
The structure of each gear tooth is essential to its performance. The addendum, the part of the tooth above the pitch circle, and the dedendum, the part below, ensure proper clearance and smooth engagement between gears. The tooth size is defined by the module, a unit that represents the pitch diameter divided by the number of teeth. The module sets the foundation for designing gears with the correct spacing and tooth count to achieve a specific gear ratio. Two mating gears must have the same module so that their tooth size, spacing, and profiles align perfectly.
Parts of a tooth like the root (the base of the tooth) and the face (the upper surface of the tooth above the pitch circle) contribute to the durability and strength of gear. These surfaces endure significant stress during repeated engagement, so their design and finishing are essential for ensuring long-lasting performance. A key factor during engagement is the pressure angle – the angle at which force is transmitted between meshing gears – which determines how efficiently and smoothly power flows through the gearset.
By carefully tailoring these elements, engineers can create systems that meet specific needs.
Types of Gears
With the exception of the castle wheel used in the keyless works, gears used in a mechanical watch are almost always spur. They are characterized by straight teeth that are aligned parallel to the axis of rotation and are ideal for transferring motion between parallel shafts. In a wheel train, they form the connection between key components, such as the mainspring barrel, center wheel, third wheel, fourth wheel and escape wheel. Spur gears can also be arranged with their axes at right angles such as the winding pinion in a movement which engages a perpendicular crown wheel during winding.
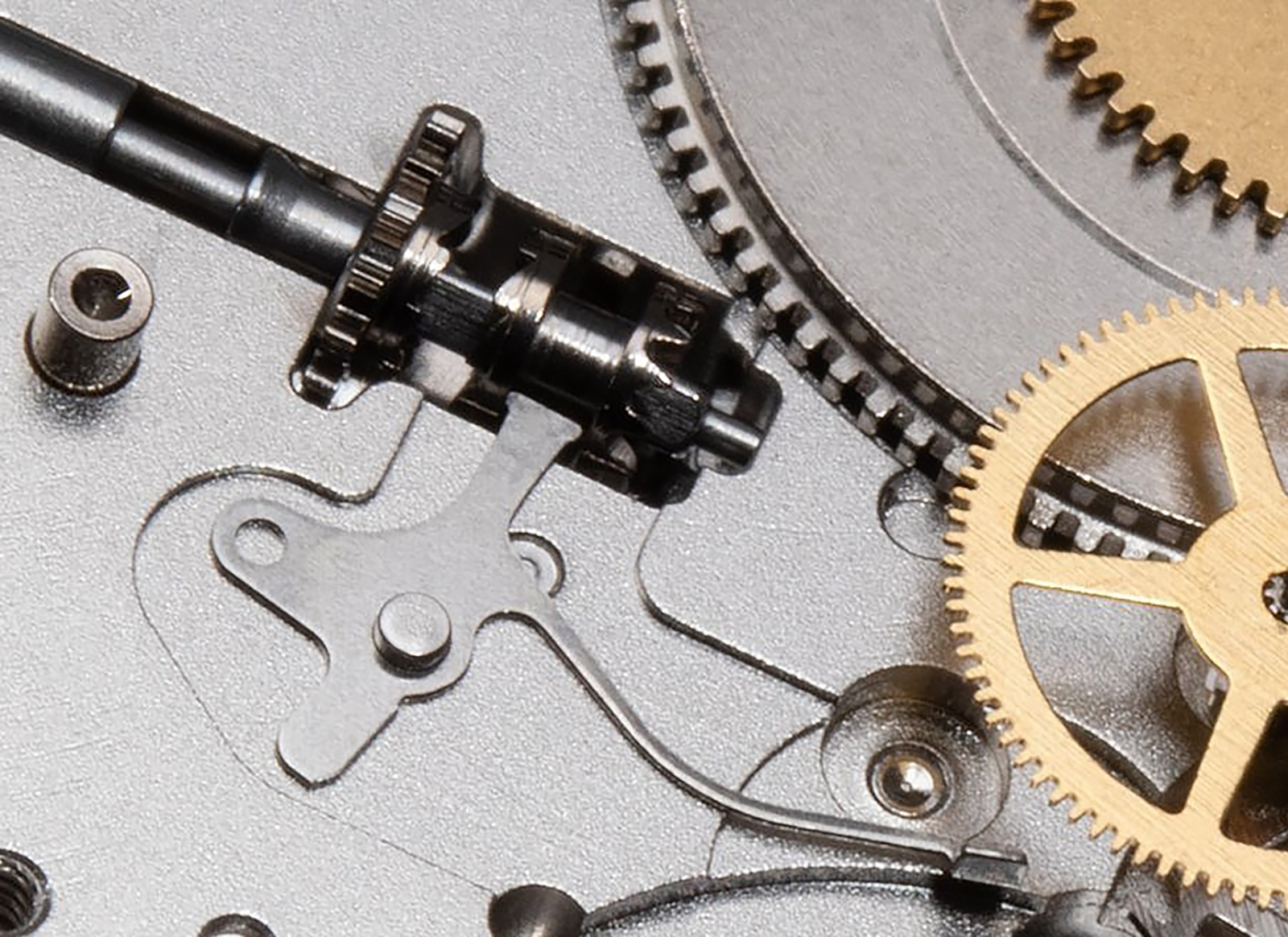
The castle gear, also known as a clutch wheel, features two sets of axial teeth on it. In the time-setting position, the inner teeth engage with an intermediate wheel that drives the minute wheel in the motion works, and in the winding position, the outer teeth mates with the winding pinion. Image: The Naked Watchmaker
The primary reasons spur gears dominate watchmaking is their compactness and efficiency in transmitting torque. Due to their simple, planar design, they have low inertia compared to helical or bevel gears and offer relatively low friction loss, which is vital for maximizing the limited energy provided by the mainspring. Additionally, spur gears are comparatively easy to manufacture and assemble, making them more suited for the tolerances required in horology.
In extremely rare cases, bevel gears are used for vertical time displays or in a differential. Bevel gears, unlike spur gears, have angled teeth and are designed to mate at non-parallel axes, often at a 90-degree angle, enabling torque transfer across different planes. However, they require more space and are far more challenging to manufacture with the precision required for watchmaking, as the geometry of bevel gears makes maintaining consistent contact points at various angles a more complex process.
An even rarer type of gear in watchmaking is the worm gear. Worm gears are used to achieve high reduction ratios in a very compact space. When the worm rotates, it engages with the teeth of the spur gear in a perpendicular orientation, allowing for significant torque increase while reducing speed.
Age-Old Rivals: Involute and Cycloidal Tooth Profiles
The two prevalent types of tooth profiles used in watchmaking are cycloidal and involute. The history of cycloidal gears is a collaborative evolution involving several prominent figures who contributed to its theory and application over time. Cycloidal gearing traces back to early geometrical explorations by Girard Desargues in the 17th century, whose work in projective geometry laid a foundation for understanding cycloidal curves, though he did not directly apply them to gears. His student, Philippe de La Hire, conducted one of the first formal analyses of cycloidal gear profiles around 1694, recognizing that cycloidal teeth could better distribute contact forces, making them ideal for clocks and minimizing wear in precision mechanisms.
Around the same period, Danish astronomer Ole Rømer may have independently explored cycloidal profiles while developing precision astronomical instruments like the Jovilabium, though his contributions are less documented. Later, in 1733, French engineer Charles Étienne Louis Camus expanded on La Hire’s work, publishing a detailed mechanical analysis that solidified the advantages of cycloids and further popularized them in clockmaking. By the mid-18th century, this collaboration of insights established cycloidal gears as the precision standard in horology, though they were eventually eclipsed by involute gears for broader mechanical applications.
Today, both cycloidal and involute profiles continue to be used in watchmaking, with each profile selected for its specific advantages. Cycloidal profiles are valued for their precision and smoothness in low torque scenarios, while involute profiles are often favored for their versatility, resilience to slight misalignments and suitability for high torque applications.
Valérien explains, “Neither the cycloidal or involute gear profiles used in watchmaking are perfect theoretically; they are adapted and modified to better suit the needs of any particular design — and those needs change and vary within the movement, so one movement is likely to contain both types of gear profiles. More modern computer analysis has allowed manufacturers to further optimize the profiles for the needs of each gear meshing.”
To understand how we got here, it helps to have a basic understanding of how each geometry is formed. The involute curve is generated from a point on the circumference of a base circle as a taut string unwinds around it, or by rolling a straight line on a base circle. Two mirror-image involutes then form the shape of a tooth, with the tooth root extending below the base circle to ensure proper meshing with another gear. The tooth root can be either square or circular; the choice of root shape does not affect power transmission. However, square roots can lead to stress concentration at the corners, potentially affecting durability under greater loads. Thus, circular roots are generally preferred in modern gear design for their strength and reliability.
While the base circle provides the foundational geometry for tooth design, the functional aspect of gearing is primarily governed by the pitch circle. In an involute gear, the pitch circle is larger than the base circle and determines how gears interact with each other during operation, ensuring that they mesh correctly and transmit torque effectively. It establishes the spacing and thickness of the teeth, which are crucial for smooth engagement and efficient power transfer.
Oftentimes, involute gears in watches tend not to resemble a classic involute (the ones found in textbooks or when you google) as either their profiles have been modified or they simply have different modules (tooth sizes) or were designed with different base diameters. Designing from a smaller base diameter will result in having more “pointed” teeth while smaller modules often result in a less distinct involute profile that appears somewhat triangular, but they are all still very much based on the involute curve.
The involute profile offers several advantages, including smoother power transmission, less sensitivity to slight variations in wheel positioning, better wear resistance and the ability to handle high torque. They are more often found in high volume watches, spanning established brands like Patek Philippe, Audemars Piguet and Rolex along with major movement suppliers like ETA and Sellita.
Valérien explains, “Involute profiles are generally cheaper to produce using hobbing techniques and are more suited to high volume production that require more expensive specialized machinery. This is why high-volume manufacturers try to use involute gears as much as they can, modifying the theoretical form of the tooth to minimize friction and loss of energy.”
Jérémy elaborates, “The great advantage of involute-based standards is their reliability. The size of watchmaking components induces geometric variations that are proportionately large in relation to their size. It is therefore essential that a gear exhibits stable behavior despite production variations, which is not possible with traditional cycloidal gearing. We should also mention the rationalization of production tools. At the beginning of the previous century, each gear required its own cutter. Today, our involute standards enable us to cut complete ranges of teeth. An 80-tooth gear can be cut with the same cutter as a 12-tooth pinion, thus limiting production tooling and simplifying processes.”
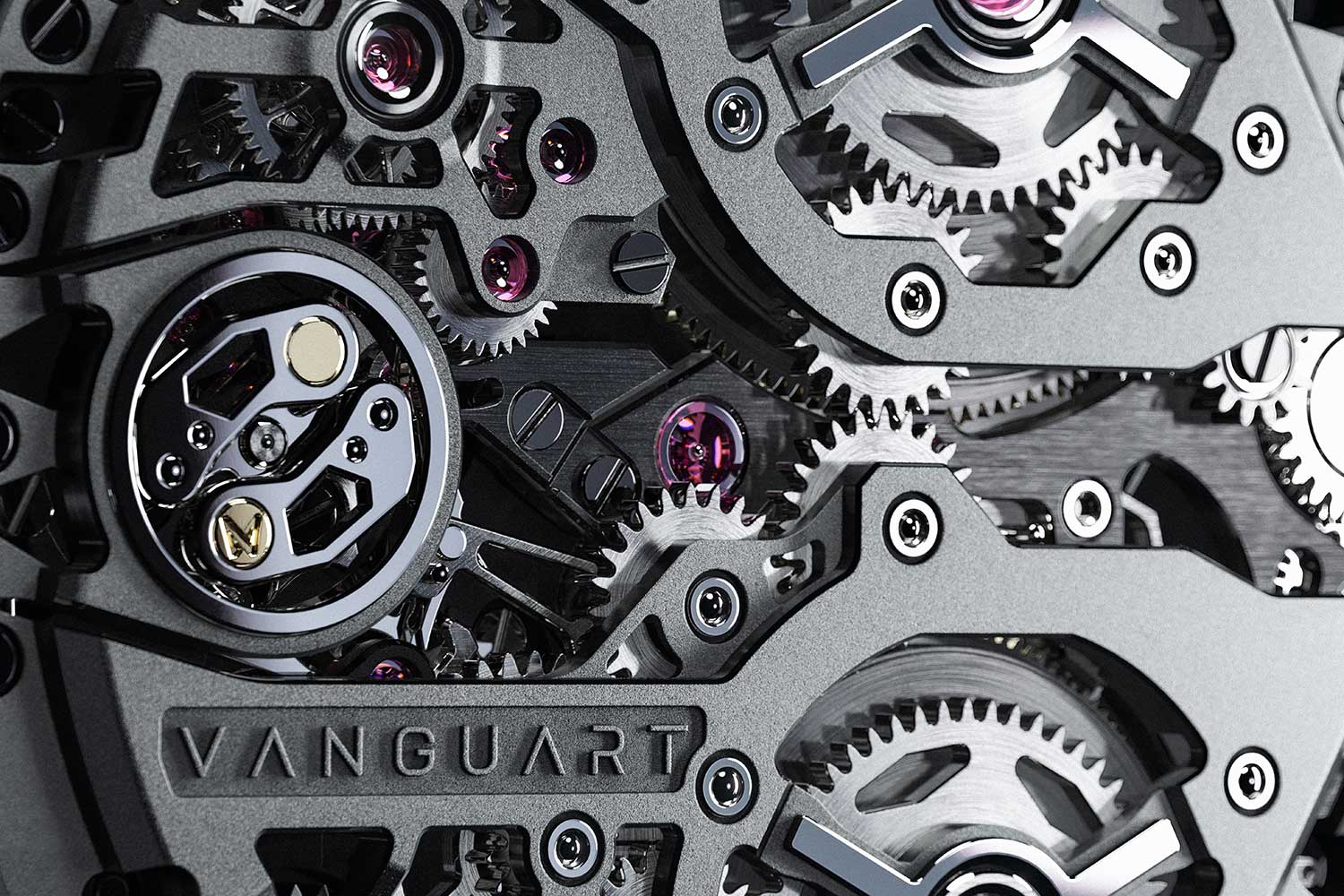
The widespread use of involute gears in the highly unusual and inventive Vanguart Black Hole Tourbillon. It features a secondary gear train and a governor, like a minute repeater, to regulate the speed of the time display (made up of three rotating discs) during time-setting. The involute profiles are designed to ensure silent operation and eliminate speed variations
“More generally, tooth profiles are adapted to the specific application. For example, we seek to minimize torque variations on certain transmissions, e.g. on a barrel and finishing gear to optimize the torque transmitted to the balance wheel or to limit gear backlash on a display gear.”
A cycloidal tooth profile, on the other hand, is created using an epicycloid or a cycloid for the addendum of the driving wheel and a hypocycloid for the dedendum of the driven pinion. An epicycloid is formed by rolling a smaller circle around the outside of the base circle of the driver, while a hypocycloid results from rolling a smaller circle along the inside of the pitch circle of the driven. This means that cycloidal profiles are designed in mating pairs.
The addendum curve typically follows a symmetrical shape, meaning each side of the tooth mirrors the other. However, symmetry is not essential for gears that rotate in one direction. As there is only one active face, the gear tooth can be asymmetrical (such as the sawtooth profile found on ratchet wheels) and tailored to the unique demands of its function. A traditional and now-trendy cycloidal tooth profile is wolf’s teeth which feature an epicycloidal curve on the active side that engages with the mating gear and a slightly concave curve on the inactive side.
An important characteristic of cycloidal gears is that the base circle also serves as the pitch circle. At first glance, involute and cycloidal gears may appear quite similar, but their differences become evident in the way they mesh. By observing how the gears mesh, one can better identify the positions of the base circle and pitch circle.
In involute gearing, the pitch circle and base circle are distinct, and the involute shape of the teeth compensates for minor changes in center distance. This design allows involute gears to maintain a constant angular velocity ratio, even if the gears experience slight misalignment. A fixed pressure angle — most commonly 20 degrees in watchmaking — ensures that as the gears rotate, the point of contact between their teeth moves along the involute curve, keeping force transmission steady and the velocity ratio constant. This straight-line contact path not only makes involute gears resilient to minor deviations in alignment but also helps self-correct these shifts during operation.
Cycloidal gearing, in contrast, has the same pitch and base circle, with meshing based on epicycloid and hypocycloid curves. This creates a rolling contact between the teeth, minimizing sliding friction and reducing wear. However, unlike involute gears, cycloidal gears do not maintain a constant pressure angle throughout engagement. The pressure angle varies dynamically as the teeth mesh, contributing to the smooth rolling engagement but also making cycloidal gears more sensitive to precise alignment. Without the self-correcting capability of involute profiles, any misalignment in cycloidal gears can disrupt the evenness of power transmission, leading to inconsistent torque and increased wear.
As a result, involute gears are more widely used especially in high volume manufacturing where slight variations are inevitable while cycloidal profiles remain preferred in more artisanal applications where consistent alignment can be guaranteed.
Jérémy explains, “There are a lot of small, independents that use cycloidal gears, and sometimes in their movement, there is one specific set of gears that is a bit more specific to address an issue. Cycloidal gears are good because they are easy to put in place; it’s easy to draw, to cut. The involute is a bit more complex, because you need to calculate the involute shape, and not everybody can do it.”
George Daniels, in his book Watchmaking published in 1981, described cycloidal gears as having “the most suitable addendum for watch train wheels.” He writes, “By careful attention to pitch diameters, pinion polishing and ‘depthing’ of pairs, the watchmaker can make a smooth running train with smooth power transmission.”
However, he points out, “The production engineer cannot bring such minute attention to bear upon every component and prefers a tooth form that will work acceptably with greater tolerances for increased simplicity of cutter design.” These challenges, Daniels notes, “have led to the introduction of modified curves based on the cycloidal system.” In these scenarios, the addendum curve is adapted, resulting in fuller tooth faces and an ‘ogival’ tooth shape. He writes, “The fuller curve has the effect of slowing the rotation of the wheel just as the following pinion leaf approaches the point of contact. But this means the leaf is slightly in advance of the approaching tooth and contact is assured without catching, which would give rise to extra friction in an imperfect depth. This allows a greater tolerance in diameters, concentricity and bearing freedom.”
Traditionally, involute gears were used mainly in the keyless and motion works where torque and tooth pressure are high. Daniels notes that “involute teeth are not suitable for the high gear ratios needed in watch trains.” He writes, “When a great disparity exists between the sizes of the driver and the driven, the pressure angle of the curves of the pinion becomes excessive and causes unacceptable friction and pressure on the pivots.”
Valérien explains that Daniels’ recommendation, taken in its context — artisanal pre-computer aided design watchmaking — is perfectly valid commentary. However, today things are less clear cut.
Jérémy elaborates, “Each era has had its own gearing preferences, dictated by technical advances and the tools available, and the certainties of one period have evolved along with knowledge. Cycloids were the best compromise available to technicians for decades. In watchmaking, the evolution towards involute gears began in the 1940s with the forerunner of modern watch gears, Mr. Heinrich Stamm. He theorized their use and standardized their design in what later became the famous ETA standards in the 1970s.”
He continues, “Mr. Heinrich Stamm’s work was carried on by one of his younger colleagues, Michel Belot, who had the opportunity to set up his own company and serve a large number of watch brands. As tools evolved over time, Michel was able to take a giant step forward thanks to IT. With computing power maximized, he was able to multiply simulations and develop tooth profiles according to use cases and conditions. Thanks to him, we now have gearing standards based on involute but adapted to the specific requirements of watchmaking.”
Valérien explains, “Both cycloidal and involute gears are relatively easy to produce using slower, more artisanal methods; however, cycloidal gears have a theoretical advantage over involute when high efficiency is required, like, for example, in the going train of a mechanical movement. Cycloidal gears are also generally taller and thinner in [tooth] profile, some value this aesthetical component, but it also makes cycloidal gears less robust than involute gears. The gear train for winding the movement, for example, does not need the same efficiency, but should withstand higher forces, so some engineers might opt for involute gears for that part of their design.”
“When engineers are choosing the profiles for their constructions, the standards are accompanied with tables of suitable gear ratios and use cases.”
The main tables are SPYR (standards of a group of companies), EVJ (standards of the Vallée de Joux Technical College); NHS (former Swiss horology standards), CETEHOR (French standards) and British Standard 978, with NIHS (Swiss watchmaking industry standards), MB (Michel Belot standards) and ETA (SMH/ Swatch Group standards) being the most dominant. There are no Japanese standards, and the profiles in a Grand Seiko, for instance, are completely tailored.
“Most companies use either Heinrich Stamm’s profiles or Michel Belot’s profiles. And the few who don’t, usually work with NIHS standards,” says Jérémy.
Creating a robust gear train with stable torque is a huge challenge, which is why many watchmakers opt to build on the proven designs of existing movements like the Valjoux 7750. As Jérémy explains, “The ETA tables are reserved for Swatch Group companies. MB standards are reserved for people working with Michel or us. While NHS, CETEHOR, etc. are available for everybody, they’re not the most robust. And creating without a table requires a lot of knowledge to do something robust. But above all, I think that not everyone is sufficiently aware of gear engineering. And it’s sometimes easier to use what already exists than to tackle such a complex field!”
In 2017, Jérémy and his colleague Axel Leuenberger founded Timeforge and took on the task to preserve the work of Michel Belot. Now retired, Belot began his career at the technical department of Ebauches SA in 1972 and notably contributed to the development of the Valjoux 7750. He later worked at ETA, as well as at SMH (now Swatch Group) before he founded his own company. Throughout his various roles, he not only established a standard for gears but also developed a software that could simulate gear profiles. The software had since been widely adopted but as Belot approached the age of retirement, he begun looking for the next generation that could carry on his work and found Timeforge. Jérémy, who is also the co-founder of Vanguart watches, had initially enlisted the help of Michel Belot to develop the gears on their Black Hole Tourbillon but he ended up rebuilding Belot’s gear simulator software.
“The software that he developed had 30,000 lines of code. So he explained to us the 30,000 lines, and we translated in a modern language to do the application that we have,” says Jérémy. The application, Gearsimulator, is provided as a subscription-based service. Although other gear simulation software exist, Gearsimulator specializes in gear design optimization, executing simulations with a processing time of one second per model while others can take up to 10 minutes. The software offers precise control over gear parameters and performance metrics.
It allows close monitoring of torque variations and speed consistency, both in forward and reverse directions. These metrics ensure that the gears operate smoothly, with minimal energy loss. It also provides a measurement of gear play, which affects the accuracy and responsiveness of a gear system. By controlling gear play within a tight range, it can optimize the engagement between gears, improving efficiency and reducing wear.
In addition to these metrics, the software monitors the contact path and radius variation, which ensures consistent meshing and minimizes wear on the gears. With an efficiency yield measurement, the software provides a clear view of the energy conservation within the system, helping to identify areas where friction loss can be reduced. The average yield, reported at 97.41 percent in the example, reflects a high level of efficiency in the gear operation, meaning that very little energy is lost due to friction or improper meshing. With options to adjust the modulus, center distance and friction coefficient, the software allows for a highly customized approach to gear design, enabling optimization of each gear pair based on specific performance requirements.
Triangular Teeth in Chronographs
A third type of tooth profile, most commonly found in horizontal clutch chronographs, is triangular teeth. To understand why this profile has become the standard, it helps to consider the mechanics of a chronograph.
The clutch wheel moves between two positions: an engaged position, where it meshes with the chronograph seconds wheel to transmit motion from the drive wheel, and a disengaged position, where it disconnects from the chronograph seconds wheel, immobilizing the hand. The transition between these states is critical to smooth operation and is often prone to unwanted movements, such as the chronograph seconds hand shifting backward or forward slightly when engagement occurs.
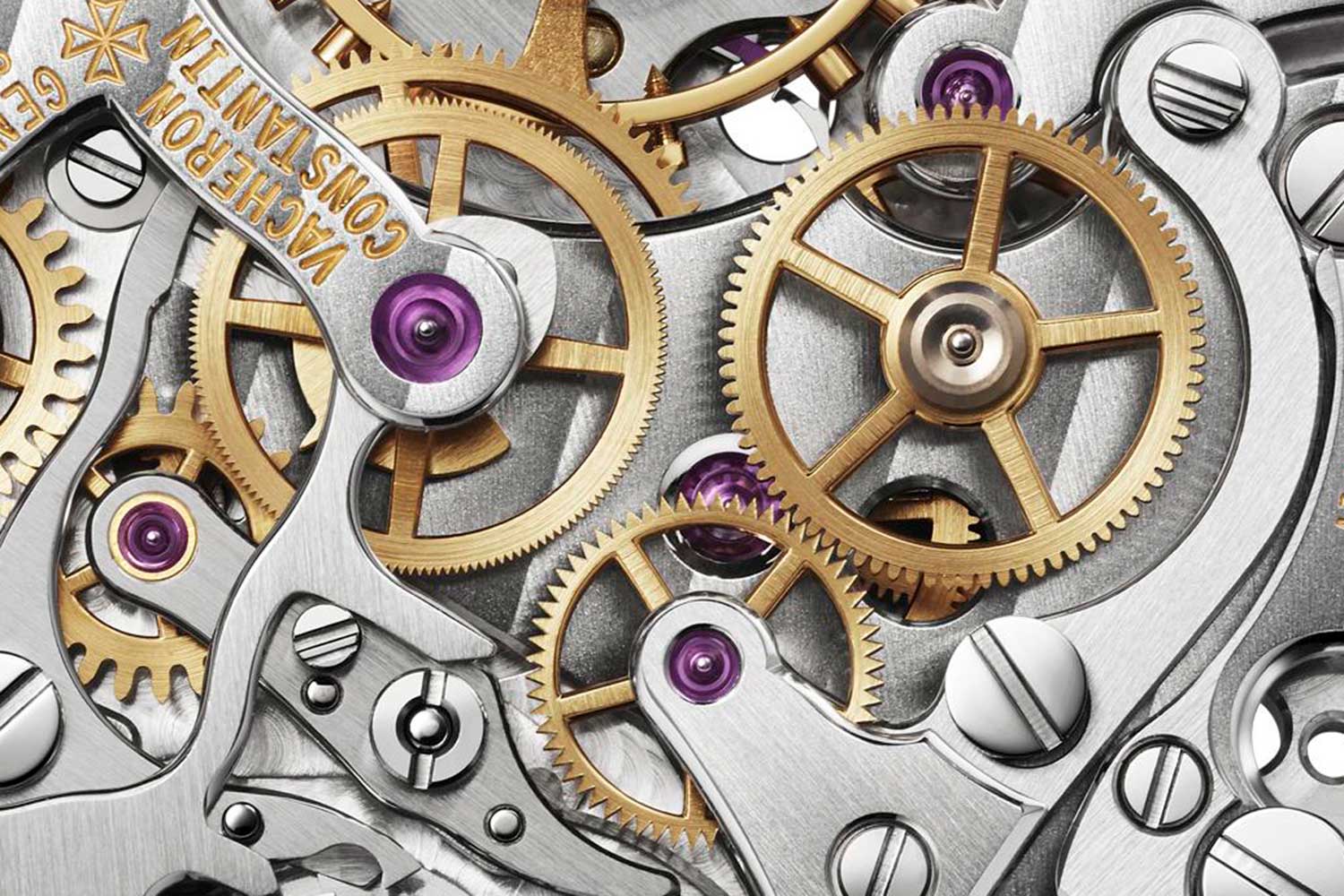
The Vacheron Constantin Caliber 1142 with classic chronograph tooth profiles - epicycloidal teeth for the drive wheel and triangular teeth for the clutch and chronograph wheels. The chronograph wheel has twice the number of teeth as the clutch wheel to increase the chances of the clutch wheel’s teeth encountering a gap, reducing the chances of the teeth clashing or failing to mesh
The teeth of the clutch wheel and chronograph seconds wheel are triangular, with straight flanks that enable them to mesh easily with each other as they come in and out of engagement. However, due to their pointed profile, triangular teeth tend to engage with more abrupt force, which causes seconds hand stutter during initial penetration. In addition, there’s a risk of point-to-point contact, which causes the tooth of the clutch wheel to slip either forward or backward into the empty space of the chronograph wheel. This is another factor that causes the seconds hand to jump either forward or backward, detracting from precision.
To reduce the risk of the seconds hand jumping unexpectedly, the chronograph seconds wheel typically has twice the number of teeth of the clutch wheel. This is to increase the chances of the tooth of clutch wheel encountering an empty space between two consecutive teeth on the chronograph wheel as both wheels come into engagement. At the same time, a tension spring lightly brakes the chronograph seconds wheel, thereby preventing flutter. This is virtually the standard on horizontal clutch chronographs, ranging from the Lemania 2310 to the A. Lange & Söhne Datograph.
However, while these solutions reduce the risk of seconds hand stutter, it doesn’t eliminate it entirely. Additionally, the meshing between triangular teeth is irregular. Unlike cycloidal or involute designs, triangular teeth concentrate stress at specific points of contact during meshing. When the clutch wheel drives the chronograph wheel, the engagement begins with the tip of the clutch wheel’s tooth pressing against the straight flank of a tooth on the chronograph wheel. As the gears rotate, this contact transitions; now, the straight flank of the clutch wheel’s tooth pushes against the tip of the chronograph wheel’s tooth.
This point-to-flank contact concentrates the forces between the teeth onto small, isolated points, rather than distributing the load evenly across the flanks of the teeth. As a result, the teeth experience intense localized pressure, which leads to increased wear. The problem is exacerbated by the braking force applied to the chronograph wheel through a friction spring, designed to minimize play and stabilize the chronograph hand. This additional load magnifies the stress on the contact points, accelerating wear on these high-stress areas. The drive wheel, on the other hand, typically has epicycloidal or triangular teeth. As it is permanently meshed with the clutch wheel, which also has triangular teeth, this also causes material wear on both wheels.
A patent filed by Patek Philippe in 2004, with Michel Belot listed as one of the inventors, offers the best solution to these issues to date. It can be found in the Patek Philippe caliber CH 29-535 PS. The invention refines the tooth profiles of all three wheels – drive, clutch and chronograph seconds.
Each tooth on these wheels is designed with an asymmetrical profile. The inactive flanks are designed to reduce play and prevent the chronograph wheel from moving backwards during engagement. They are specifically shaped to align with the natural engagement trajectory of the gear teeth. When the clutch and chronograph wheels are engaged, the radial axes of the teeth of both wheels align, and the peaks of the teeth make contact along a path that prevents unwanted motion. The inactive flank of each tooth follows this penetration path, ensuring that the teeth enter engagement smoothly without causing a misalignment that could result in the chronograph hand jumping unexpectedly.
Furthermore, the active flanks of the teeth on all three wheels – drive, clutch and chronograph wheels – are given a curved profile. This shape promotes smoother engagement by ensuring that the contact between the teeth is not abrupt or localized, as in traditional triangular teeth. Instead, the convex shape allows the teeth to mesh with a broader contact area along the flanks, reducing point-to-point pressure, wear and torque fluctuations.
In essence, the patent achieves two primary objectives: (1) it minimizes the risk of unwanted movement of the chronograph hand during engagement by carefully shaping the inactive flanks to follow the natural trajectory of meshing teeth, and (2) it improves the overall quality of meshing by using convex active flanks to ensure consistent and even contact, which reduces friction, wear and torque irregularities. This impressive innovation in tooth design effectively resolved long-standing mechanical disadvantages in a horizontal coupling system.
Materials and Advancements
Brass is a classic choice for watch gears due to its relatively low cost, ease of machining and resistance to corrosion. Brass gears are durable yet soft enough to prevent excessive wear on mating parts, which is beneficial for the longevity of the movement.
Steel is often used in high-stress parts of the movement, such as the winding wheels, due to its strength and wear resistance. Certain wheels might be solid rather than spoked to withstand high torque. The pinions in a gear train are also made of steel as pinions are much smaller gears, with a lower tooth count, meaning they endure higher stress at the points of contact with their meshing gears.
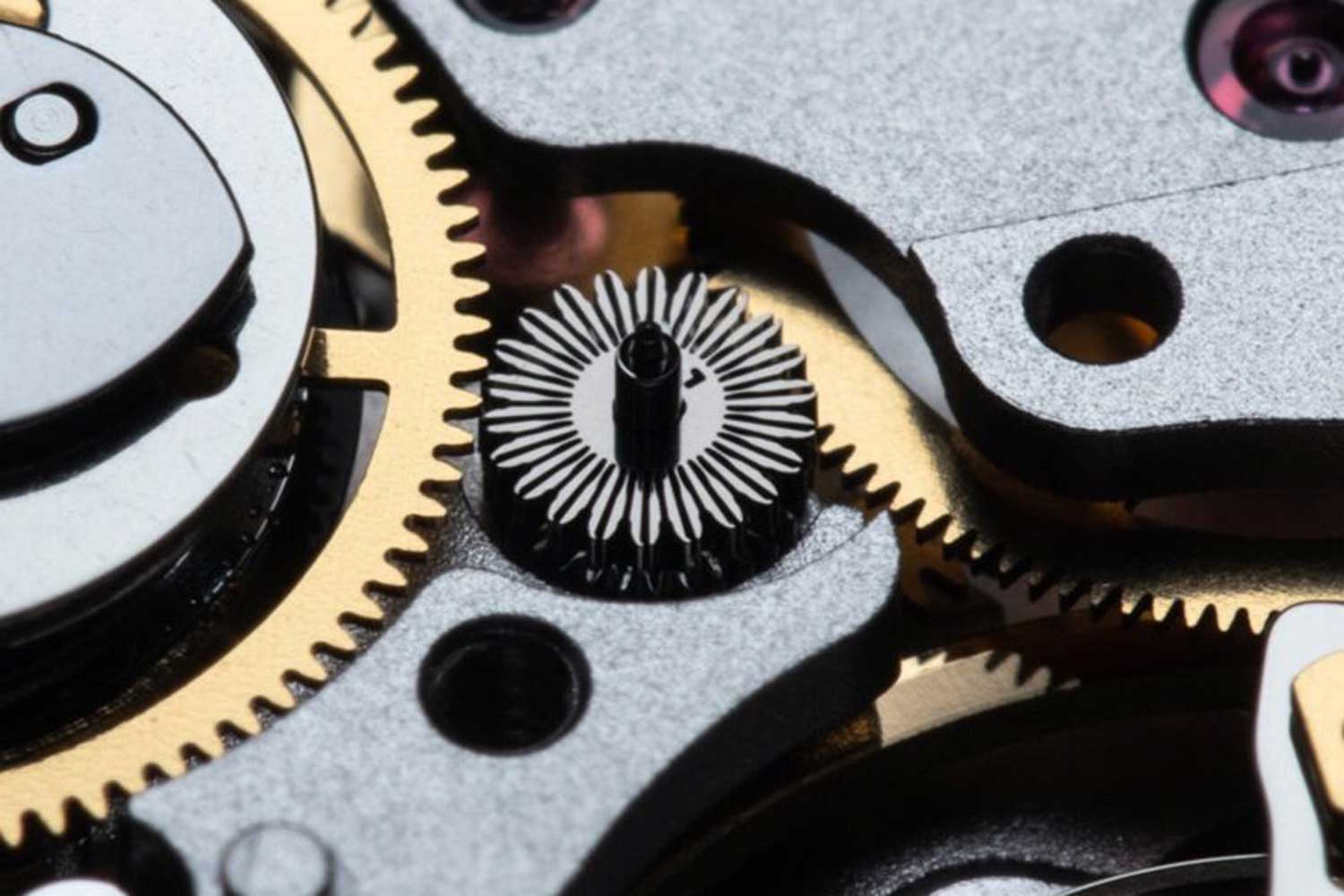
A pinion that connects the fourth wheel in the movement to the chronograph seconds wheel in the Breitling B01. It has split teeth whereby the two halves of each tooth can move slightly relative to each other, enabling them to adapt to variations or misalignments, thereby absorbing play. (Image: The Naked Watchmaker)
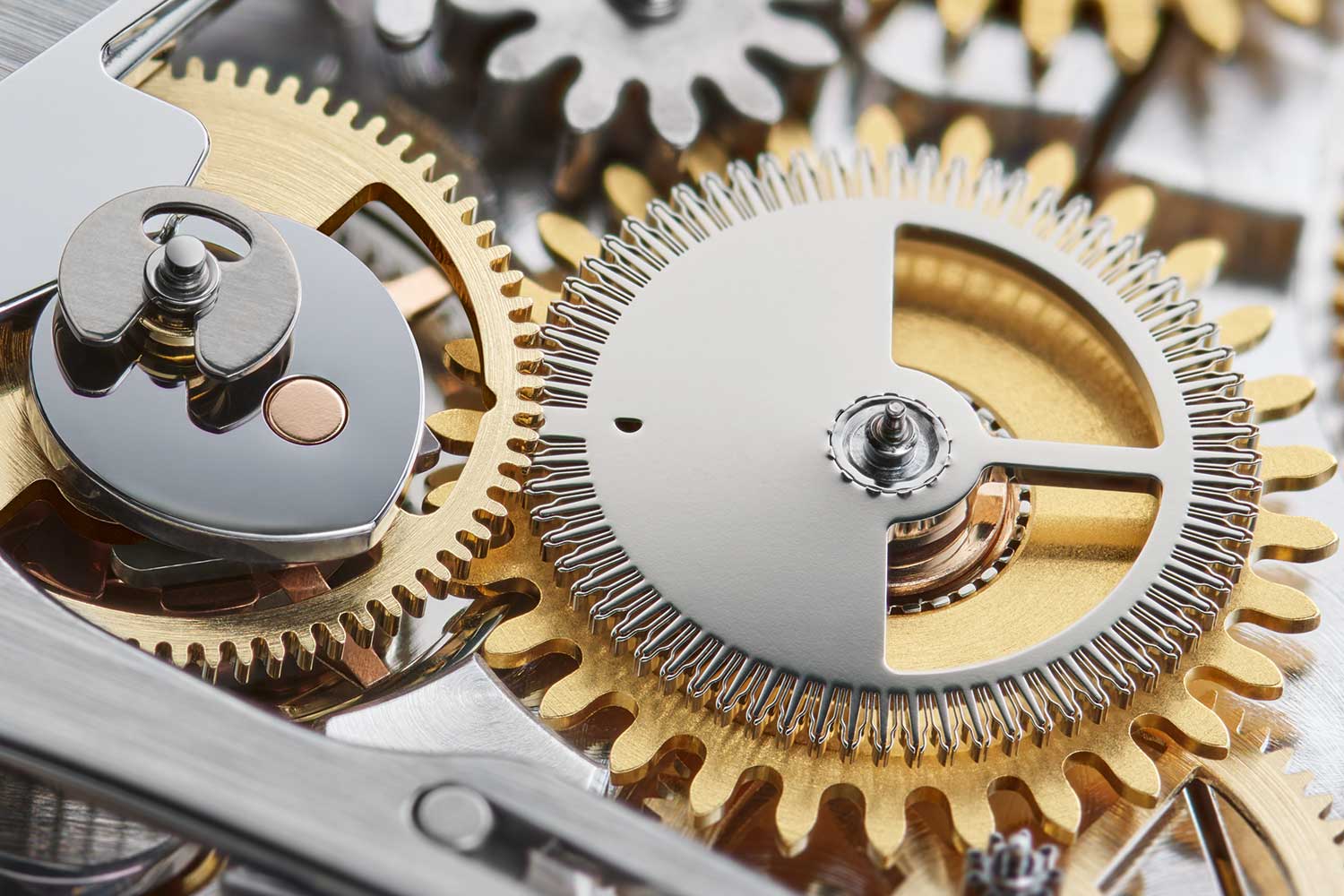
The chronograph seconds wheel with sprung teeth in the Rolex Caliber 4130. Both the Breitling B01 and 4130 are vertical clutch chronographs. However, the fourth wheels in both movements are not located in the middle and hence do not drive the chronograph wheel directly. As such, these reactive tooth profiles are required to prevent seconds hand stutter
Today, materials like nickel-phosphorus are revolutionizing gear design. Nickel-phosphorus gears are lightweight, highly durable and offer a smooth finish that reduces friction. The electroforming process used to create nickel-phosphorus components allows for extreme accuracy and complex shapes, making it possible to engineer gears with intricate, micro-scale profiles that traditional machining techniques could not achieve.
One development in high precision gears is the introduction of reactive, spring-loaded tooth profiles. Unlike traditional fixed-tooth profiles, spring-loaded gears can adapt slightly under load, adjusting their meshing based on the torque applied. This innovation reduces backlash and ensures continuous, uniform power transmission. The flexibility of the spring-loaded design also allows the teeth to respond dynamically, absorbing minor misalignments and thus improving overall efficiency and wear resistance.
Ultimately, today, gear design is a triumph in computer modeling, engineering and material science. While standard tables remain foundational, modern simulation tools have enabled watchmakers to push beyond conventional limitations, allowing them to predict and monitor gear dynamic health, tailor profiles to tighter needs and reduce the need for extensive testing. It’s a reminder that in watchmaking, even the most unassuming parts hold the weight of an age-old pursuit for perfection.